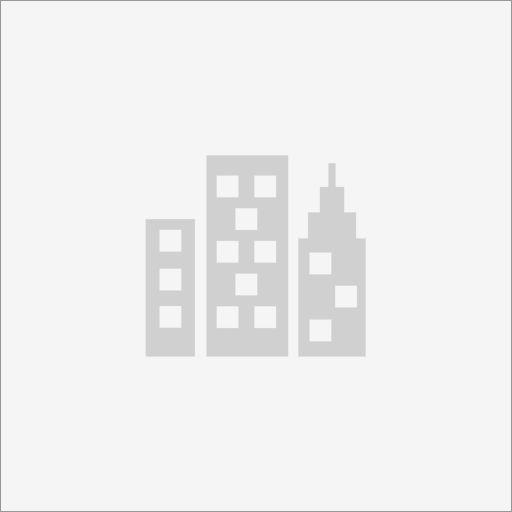
Modine - Climate Solutions
About us With more than 100 years of excellence in thermal management, Modine provides trusted systems and solutions that improve air quality and conserve natural resources. Modine is a global corporation with headquarters in Racine, Wisconsin (US), FY2022 Sales over $2.1 billion and over 11,000 collaborators worldwide. Continuous Improvement Leader Job description: This position is responsible for leading enterprise projects and executing the business process LEAN deployment plan in support of the LEAN transformation. This person will serve as a Continuous Improvement leader providing expert advice associated with LEAN plans, recommendations, communication, marketing and deployment. Responsibilities: Participate in the development and implementation of LEAN business process strategies and tactical execution. Lead implementation of initiatives supporting business process capability improvement through waste, variability and lead time reduction, utilizing process improvement methodologies that deliver sustainable results. Develop best practice sharing across functional areas. Track and monitor full and consistent implementation. Act as an internal cross-functional expert providing guidance and consultation supporting the Modine LEAN Transformation. Specific areas of focus include: Leader for deployment of needed LEAN knowledge including the deployment of LEAN tools, processes and mental models, i.e.; Kaizen, 5S, value stream mapping, etc. Support establishment and communication of the LEAN philosophy, leadership culture and needed behaviour changes. Define tactics and methods to foster employee engagement, successful change management and acceptance. Facilitate workshops and/or other forums to focus improvement, transfer knowledge, and engage team members, managers and leaders in activities supporting the business process LEAN transformation. Provide leadership in the anticipation, recognition, definition, and resolution of problems / opportunities associated with the Modine LEAN transformation. Surface methods to assess LEAN readiness and progress. Surface and recommend staff organizational requirements to deploy and sustain LEAN thinking, systems and tools. Establish and maintain method to identify and report cost savings resulting from LEAN deployment. Provide leadership to fully leverage external and internal benchmarking and standardization. Support the identification, selection and coordination of internal and/or external resources needed to support a LEAN transformation. Alignment on metrics and goals with Extended Lean Teams. Provide support on training, roadmap development and end to end processes where necessary. Internal and External customer satisfaction. Compliance with ISO requirements Be prepared to work some extended hours, when necessary, to complete a task. Be able to work in a team environment and demonstrate support of Meggitt lean principles; teamwork, cooperation, respect, and integrity. Accomplishment of project objectives and completion of assigned tasks on schedule and within budget. Collaborate with peers and supervisors to determine key goals and objectives, and corresponding metrics, to be completed during a determined period (usually one year). Review and amend these actions as appropriate. Focus on timely achievement of these goals and objectives. Primary working relationships & interfaces: Key relationships include interface with other LEAN teams, interface with continuous improvement initiative sponsors, member of business services continuous improvement team, provide direction to functional support areas (procurement, contracts, marketing, finance, information technology, legal and trade compliance, human resources) on continuous improvement efforts. Key skills and competencies required: Proficient with Lean, Cellular, and Continuous Improvement concepts, and able to implement them to increase productivity and remove waste. Experience as a Production, Manufacturing, Operations Leader or as a LEAN/CI/Six Sigma Specialist is essential Ability to analyze data from mechanical components to implement improvements to increase the reliability of the components, minimizing the assembly and test cycle time, document processes and transition operations from one plant to another when needed. Minimum degree in Engineering, Business or other related field, or equivalent experience. PhD or MBA is a plus. Six Sigma black belt is a plus. Change management and project management expertise with a track record of implementing results. Working knowledge of LEAN thinking, systems, and tools. Customer interface understanding/experience desirable. Willing to challenge the status quo and facilitate different perspectives to drive solutions. International experience is desirable, but not necessary. Experience in Lean Manufacturing, Kaizen events, and continuous improvement techniques. Familiarity/experience with continuous improvement and Six Sigma methodology. Good technical writing and presentation skills. Good verbal and communication skills. Proficiency with computer based methods and tools. Familiarity with SPC, statistical process control principles and methods Important Skills / Competencies: Ability to work with all levels of the organization, influence leaders to change / adopt change, build trust and credibility quickly Working knowledge of ISO-9001. Strong collaboration and team work skills. Ability to work in a matrix organization driving collaboration across businesses and functions with minimum supervision. Demonstrated positive energy to promote employee engagement and drive results. Demonstrated passion to drive change and challenge status quo. Demonstrated ability to lead implementation and contribute to the development of vision and strategy. Cross cultural effectiveness. Demonstrated problem solving and analytical skills. Demonstrated facilitation skills. Demonstrated business intuition skills. Ability to communicate clearly through written and oral communications. Understands functional processes and can navigate systems to extract needed data J-18808-Ljbffr
Per candidarti a questo lavoro visita www.adzuna.it.